こんにちは、ものづくりが好きなライターの淺野です。
僕は10年ほど前に初めて3Dプリンターに出会ってから、いろいろなマシンに触れてきました。その多くはフィラメントを溶かして重ねていくFDM(熱溶解積層)方式か、液体のレジンを固めていくSLA(光造形)方式で、粉末状の素材を焼き固めていくSLS(粉末焼結積層)方式の3Dプリンターを使ったことはありませんでした。
造形の特性上、どうしても大掛かりになりがちなSLS方式の3Dプリンターですが、最近では少しずつ導入のハードルも下がってきているようです。「せっかくだし、一度くらいは使ってみたいなぁ」と思っていたところ、Yokoito Additive Manufacturing(YAM)さんから「YAMで扱っているSLS方式プリンターを紹介してくれないか?」とお声がけいただきました。
これは願ってもないチャンス!ということで、京都のYAMオフィスに訪問。低コストで品質の高いマシンとして多くのユーザーに利用されているという、Formlabs社のSLS方式3Dプリンター「Fuse 1+(フューズ1プラス)」を体験させてもらいました。この記事では、SLS方式の3Dプリンターに馴染みのない方のために、 「Fuse 1+」の利用フローや扱える素材の特徴を紹介していきます。
「Fuse 1+」の利用フローをご紹介
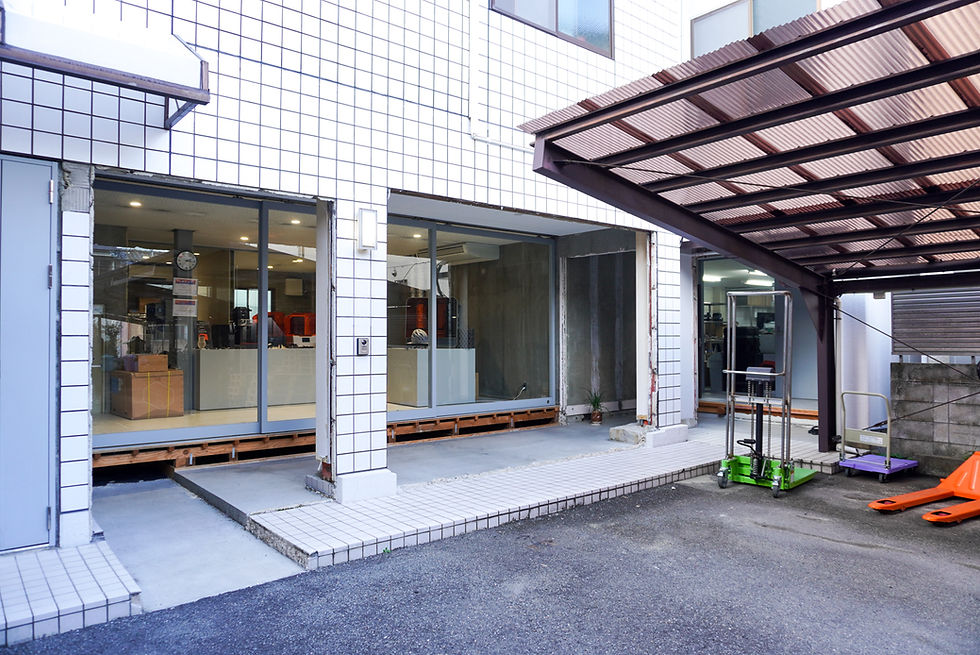

やってきたのはYAMのオフィスやショールーム、ファクトリーを兼ねた活動拠点
Yokoito Additive Manufacturing Center。その一画、5メートル四方ほどの空間に「Fuse 1+」2台と、造形物を後処理するための「Fuse Sift」が並んでいます。初めて見た「Fuse 1+」は、そのサイズやカラーリングから、おしゃれな冷蔵庫のような印象でした。
SLS方式の3Dプリンターは粉末状の素材(パウダー)を扱うため、利用エリアを区切った上で、防塵マスクを着用した状態で利用する必要があるそうです。本格的にSLSを使うのであれば、専用の部屋やガレージの一角を区切るなど、空間としての準備も必要になりそうですね。
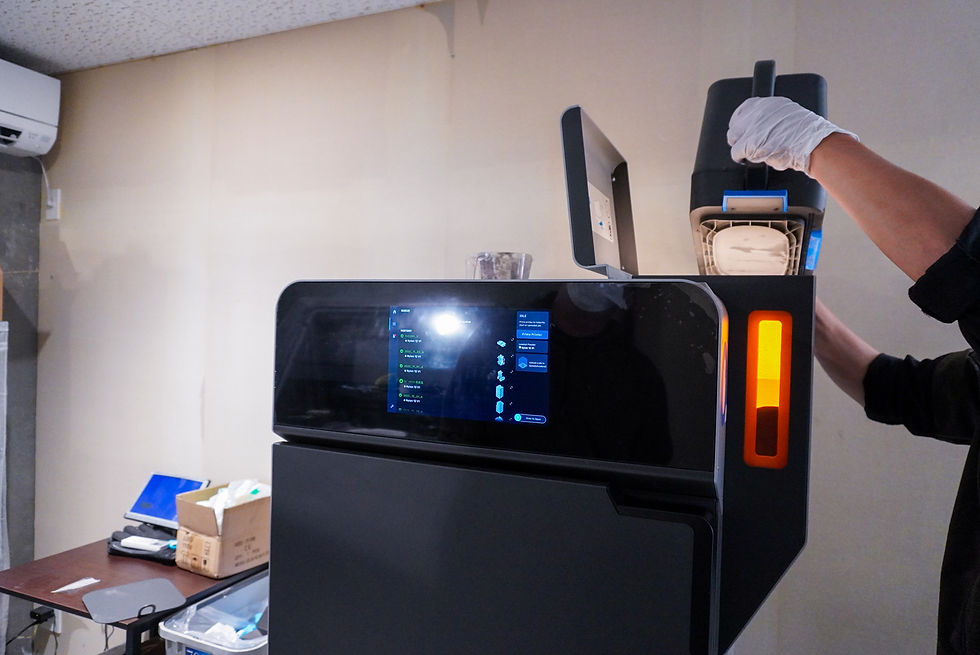
それでは早速「Fuse 1+」の使い方を見ていきましょう。まずは右上のホッパーにパウダーをセットして……
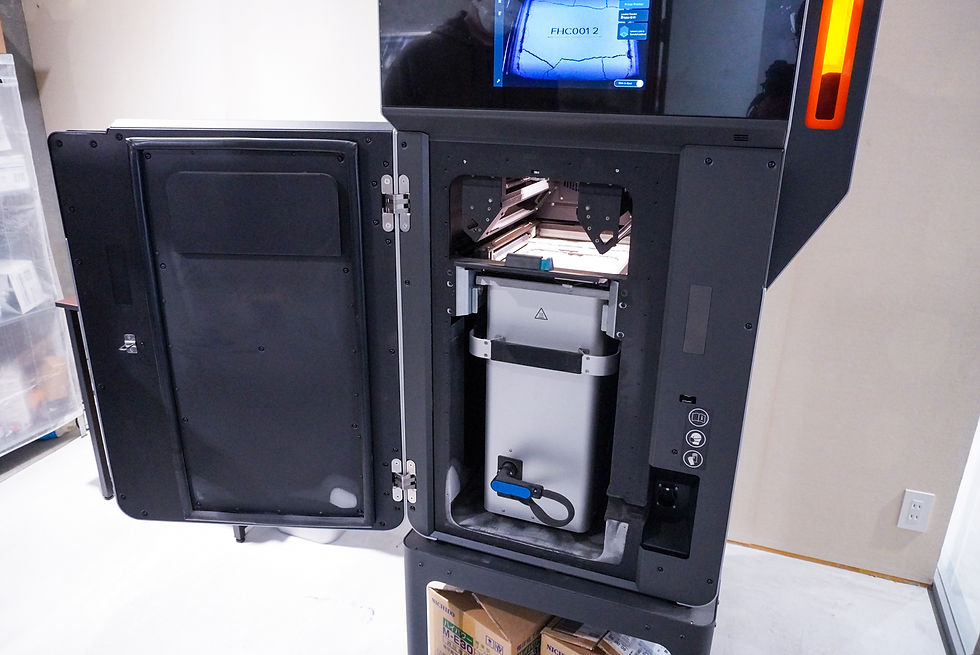
手前の扉を開けて、実際に造形が行われるエリアとなる「ビルドチャンバー」を設置します。ビルドチャンバーと本体はケーブルで接続され、造形に必要な情報がリアルタイムでやりとりされるようです。

印刷用のデータは、専用ソフトウェア「Preform」で制作。3Dデータや利用する素材を選択すると、造形時間や素材の利用率が見積もられるので、条件に過不足がないかチェックしておきましょう。完成した印刷用データは、ネットワーク経由で「Fuse 1+」本体に送ります。
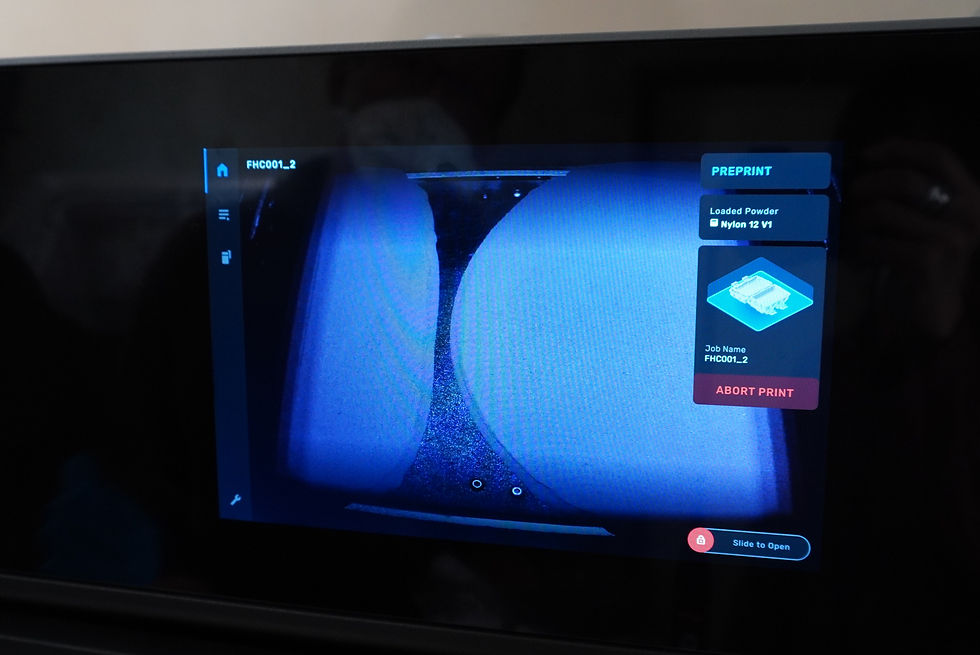
印刷をスタートすると、まずは庫内が温められます。一定の温度に達したら、ビルドチャンバーに一層分のパウダーが敷かれ、レーザーで必要な箇所を焼き固めたら、また一層分のパウダーが敷かれ……という工程を繰り返し、3Dプリントが進行していきます。
印刷中の様子は「Fuse 1+」本体のディスプレイでリアルタイムに見ることができます。暗い庫内で徐々にビルドチャンバーのテーブルがせり上がってくる様子は、大型のエレベーターを見ているような感覚でした。

印刷が完了したら、ビルドチャンバーを取り出しましょう(けっこう重い!)。この状態ではビルドチャンバー内で焼き固められた造形物と加工されていないパウダーが混在しているため、後処理を行っていきます。

「Fuse 1+」専用パウダー回収ステーション「Fuse Sift」にビルドチャンバーをセットすると、造形物が含まれたパウダーの塊がせり上がってきます。四角いその姿は「ケーキ」と呼ばれているのだとか。

バキュームをONにして粉塵を吸い込みながら、ブラシや金具などを使って、余計なパウダーを取り除いていきましょう。
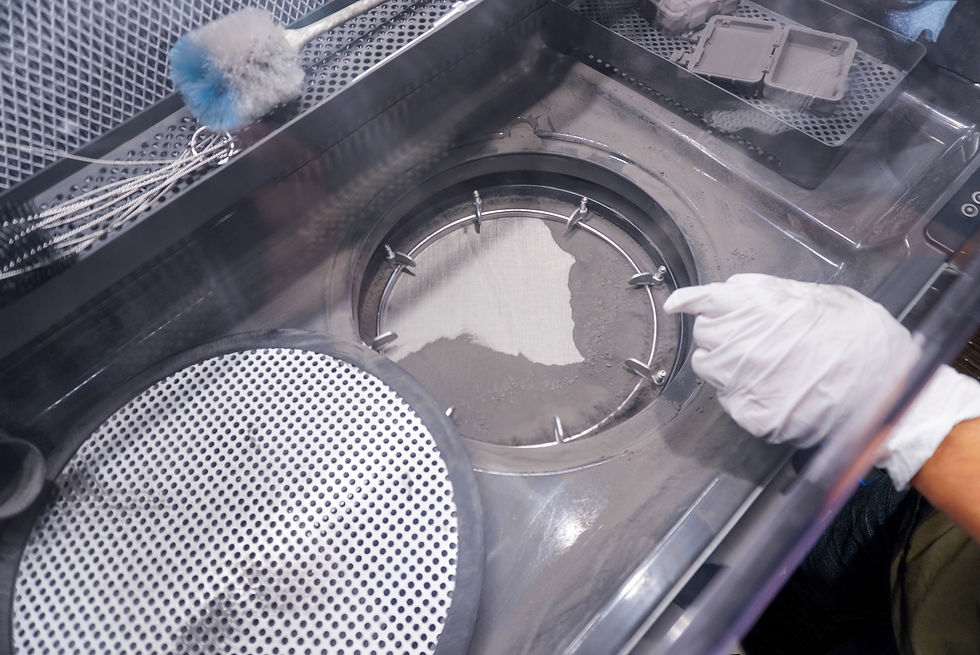
「Fuse Sift」で取り除かれたパウダーは、細かくふるいにかけられて……
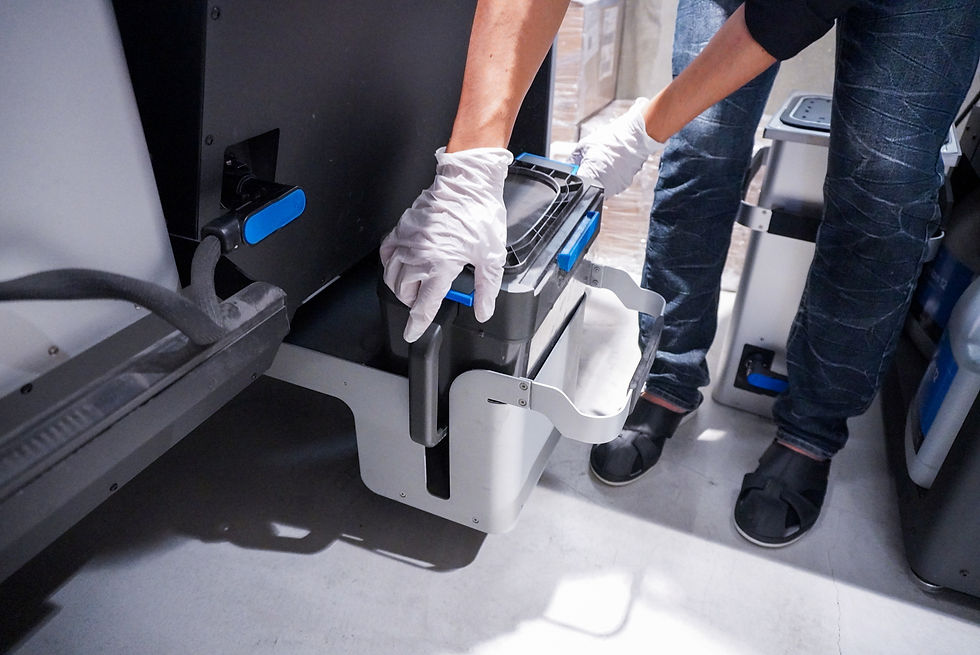
専用の「パウダーカートリッジ」に収集されます。こうして集めたリサイクル素材と新しい素材を規定の割合でミキシングすると(混ぜる作業も「Fuse Sift」で行える)、再び「Fuse 1+」で3Dプリントするための素材となります。
材料の無駄が少なく効率的に使えるのは、SLS方式ならではの特徴ですね。「『Fuse 1+』で造形 →『Fuse Sift』で後処理 → 素材をリサイクル」という循環が想定されているのは、「Fuse 1+」ならではの新しさだと感じました。
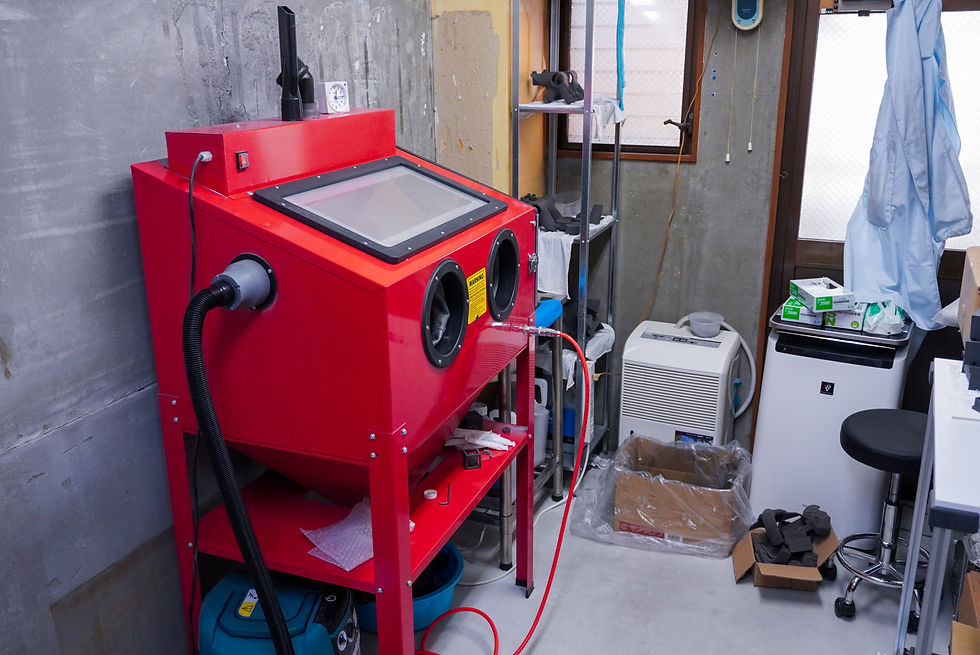
さらに細部の粉末を取り除いたり、表面を綺麗にしたりするために、サンドブラスターなどの機材を使って仕上げていきます。YAMでは市販のサンドブラスターを利用していましたが……これがなかなか難しい!
片方の手で造形物を持ち、もう片方の手でエアーと研磨剤を吹き付けていくのですが、力加減や仕上がりのタイミングがうまく掴めません。僕はあえなく途中で脱落し、YAMの熟練スタッフに頼ることとなりました。仕上げ道は奥が深い。
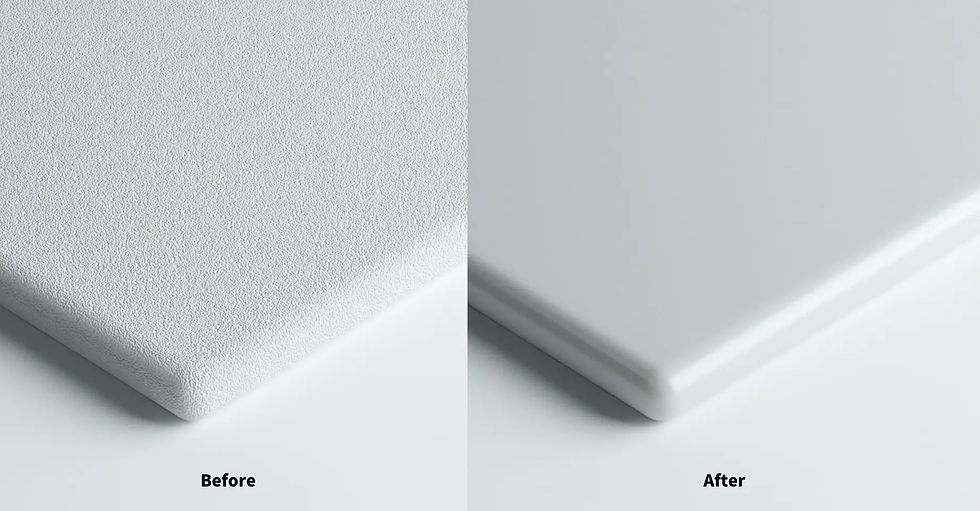
ちなみに、YOKOITO は3Dプリンターで造形した部品のクリーニング・表面処理・染色後処理システムを開発する、ドイツのDyeMenssion社とパートナー契約を結んでいます。今後は、国内総代理店としての販売、及び自社内でのシステム運用も行う予定とのことで、仕上げに不安がある僕のような人にとっては、とても嬉しいニュースですね。
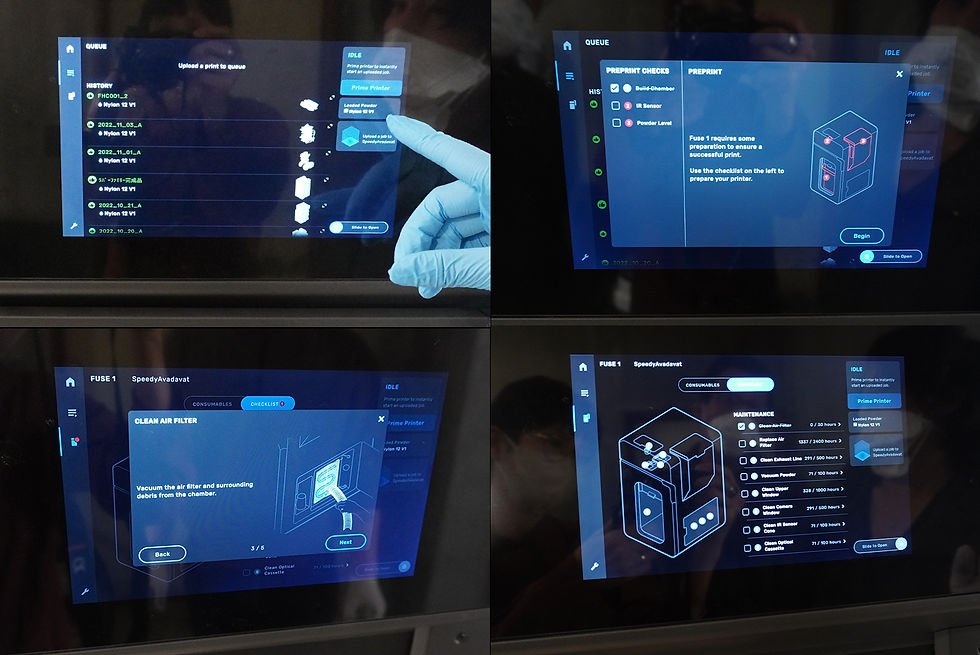
……というわけで、セットアップから仕上げまで「Fuse 1+」の使い方を紹介しました!
初めての体験でしたが、機材の準備から清掃まで、自分が何をすべきかという情報が毎回ディスプレイに表示されるので、説明通りに行動すれば戸惑うことはないだろうな、と思える親切なつくりが印象的でした。
とくに新しさを感じた「セットアップ → 造形 → 後処理 → 素材のリサイクル」という流れも、初心者ユーザーでもレクチャーを受ければ1日で習得できるそうです。SLS方式の3Dプリンターとはいえ、使うハードルはそれほど高くないのかもしれませんね。
「Fuse 1+」で扱える素材
さてさて、そんな「Fuse 1+」で扱える素材は、2022年1月時点で4種類。それぞれ特性が異なるため、素材ごとの特徴とおすすめの用途を聞いてまとめてみました。なお、異素材の混入による造形エラーを防ぐため、1素材につき1台のプリンターでの運用が想定されているそうです。
① Nylon 11 Powder

延性が高く、頑丈な部品の造形が可能です。「Nylon 12 Powder」と比較すると、柔軟性と弾力性が高いため、薄い壁やバネのような構造の造形にも向いています。
② Nylon 11 CF Powder(従来機「Fuse 1」非対応)

ナイロンと炭素繊維(カーボンファイバー)の長所を備えた、軽量かつ強靭な素材です。自転車のブレーキのような、繰り返しの衝撃に耐える高剛性部品の製造に適しています。また、Nylon 11 CFを使って造形をする際には、窒素充填装置の設置が必要になるため、従来機の「Fuse 1」ではご利用いただけません。
③ Nylon 12 Powder

強度とディテールのバランスが取れている「Nylon 12 Powder」。機能的なプロトタイプや、複雑で頑丈さが求められる最終品の両方に対応できるパウダーで、自転車のペダルなどに利用されています。
④ Nylon 12 GF Powder

「Nylon 12 Powder」と比較して、剛性と耐熱性が向上し、製造業における過酷な環境に耐えられるように開発されたガラス繊維強化材料です。頑丈な治具や固定具、強度や耐熱性が求められる配管やソケットなどに向いています。
まとめ
以上、「Fuse 1+」の使い方と素材別の造形サンプルを紹介しました。SLS方式の3Dプリンターを利用するイメージがつかめていたら幸いです。
「Fuse 1+」の資料や造形サンプルをご希望の方は、ぜひYAMにお問合せください!
<本件に関するお問い合わせ窓口>
平日 10:00-13:00・14:00-17:00
Mail: sales@yokoitokyoto.com
TEL: 075-354-6424
Comments