
はじめに
Formlabs最新大型光造形3Dプリンター「Form 4L」は、Form 3Lの後継機として登場し、技術面での大幅な進化を遂げています。
独自のLow Force Display(LFD)技術を採用し、造形速度やプリント成功率が格段に向上。また、消耗品のコスト削減や耐久性の強化も実現し、効率的な生産をサポートします。
本記事では、この二つのモデルを比較し、Form 3LでのナレッジがどのようにForm 4Lに反映されているかをご紹介します。
造形技術の比較

▲Form 4Lに搭載されているLow Force Display(LFD:左)は造形エリアに均一にレーザーが照射され、Form 3Lに搭載されているLow Force Stereolithography(LFS:右)は応力を最小限に抑えながらレーザーユニットが左右に動く仕組みとなっている
Form 3Lは、Formlabs独自のLow Force Stereolithography(LFS)技術を採用しており、造形中のパーツにかかる応力を最小限に抑えつつ、高精度なプリントが可能です。
この技術は、パーツがプリント中に受ける力を減少させることで、微細なディテールを持つ部品でも形状崩れを防ぎ、優れた表面仕上げを実現します。
一方、Form 4Lは、新たにLow Force Display(LFD)技術を搭載し、より高度な造形制御が可能になっています。
この最新技術は、従来のSLA方式とは異なり、Masked Stereolithography(MSLA)方式を基盤にしています。
LFD技術では、60個のLEDバックライトから16mW/cm²の業界最高クラスの紫外線が、LPU 4にあるレンズアレイを通じて造形エリア全体に均一に照射されるため、スピードと精度を同時に実現します。
さらに、LFD技術では、造形物とレジンタンクのフィルムとの剥離プロセスも工夫されており、特殊な二層フィルム構造のレジンタンクとLPU 4の表面構造により、剥離時の抵抗を最小限に抑え、迅速かつスムーズなプリントを可能にしています。
LFD技術により、Form 4Lは、従来のモデルと比べてプリントの成功率が向上し、特に高精度や高速プリントを必要とする生産環境での一貫性と効率性が大きく向上します。また、長時間のプリントにも安定して対応できるため、より大規模で複雑なプロジェクトにも適しています。
造形サイズ
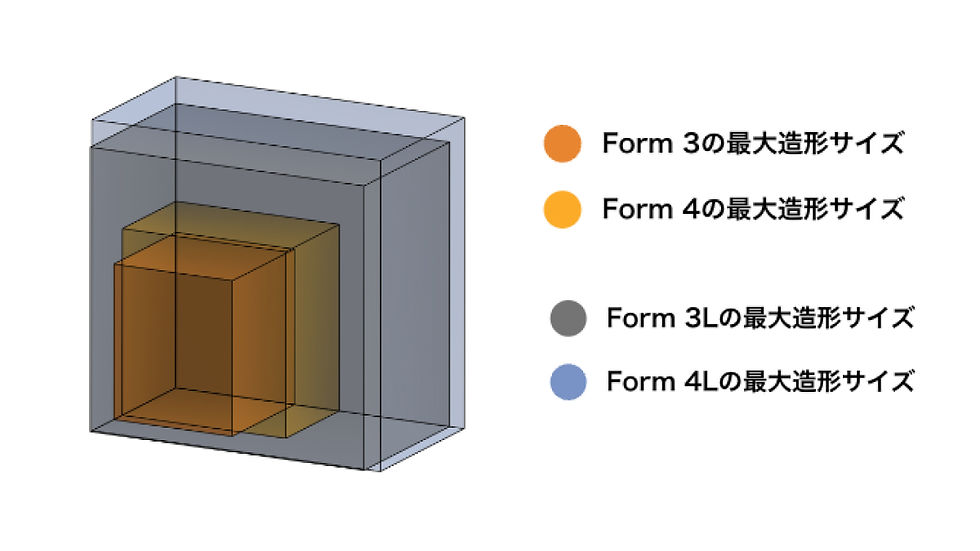
3Dプリンターの選択において、造形サイズは非常に重要な要素の一つです。Form 4LはForm 3Lに比べ、さらに造形サイズが大きくなりました。
Form 3Lは、335×200×300mmの造形サイズを提供していましたが、Form 4Lはさらに大きな353×196×350mmの造形サイズを提供し、より大型のモデルや複数のパーツを一度にプリントすることが可能です。
この広い造形範囲は、特に産業用途や大規模なプロジェクトで真価を発揮します。大きなパーツの製造はもちろん、部品の一括生産にも対応できるため、製造効率を劇的に向上させます。
造形サイズ(WxDxH):
Form 3シリーズ 145 x 145 x 193 mm
Form 4シリーズ 200 x 125 x 210 mm
Form 3Lシリーズ 200 x 335 x 320 mm
Form 4Lシリーズ 353 x 196 x 350 mm
造形速度と効率

Form 4Lは速度において飛躍的な向上を遂げており、Form 3Lの3倍〜5倍の速度でプリントが可能です。
これはFormlabsの革新的なLFD技術により実現されており、最大で80mm/時間の高速造形を誇ります。
このスピードは、1日のうちに試作や検証を複数回行うことを可能にし、製品開発のサイクルを大幅に短縮します。迅速なフィードバックとプロトタイプの改良が必要な場面では、Form 4Lの高速造形が生産効率を飛躍的に向上させ、開発プロセス全体を加速させます。
このように、Form 4Lはスピードが要求される場面で真価を発揮し、特に多品種少量生産や頻繁な設計変更が必要な業務において、時間とコストの両方を効率化する理想的なソリューションとなります。
コスト面での比較

3Dプリンターの導入において、初期コストだけでなく、日々の運用にかかるコストも重要な要素です。特に消耗品の管理は、長期的なコストパフォーマンスに大きく影響します。
Form 4Lは消耗品の耐久性とコスト効率が大幅に改善されています。特に消耗品の設計は、より長寿命であり、交換頻度が少なく済むため、運用コストを抑えることが可能です。
特にForm 4L専用レジンタンクは最低75,000レイヤーの造形に耐えることができ、頻繁な交換を必要とせず、耐久性を持たせることでランニングコストが削減されます。
また、全体的にForm 3Lと比較して約40%のコスト削減が実現されており、高性能を維持しながらも、日々の消耗品コストを大幅に削減できます。これにより、長期的なコストパフォーマンスが大幅に向上し、ユーザーは効率的かつ経済的な運用が可能になります。
このコスト効率の向上は、特に頻繁なプリントや大量生産、また材料を多く使う大型モデルの造形において大きなメリットをもたらし、企業のコスト削減にも貢献します。
高いパフォーマンスを維持しながら、総合的なランニングコストの抑制ができる点で、Form 4Lは経済的な3Dプリンターと言えるでしょう。
まとめ
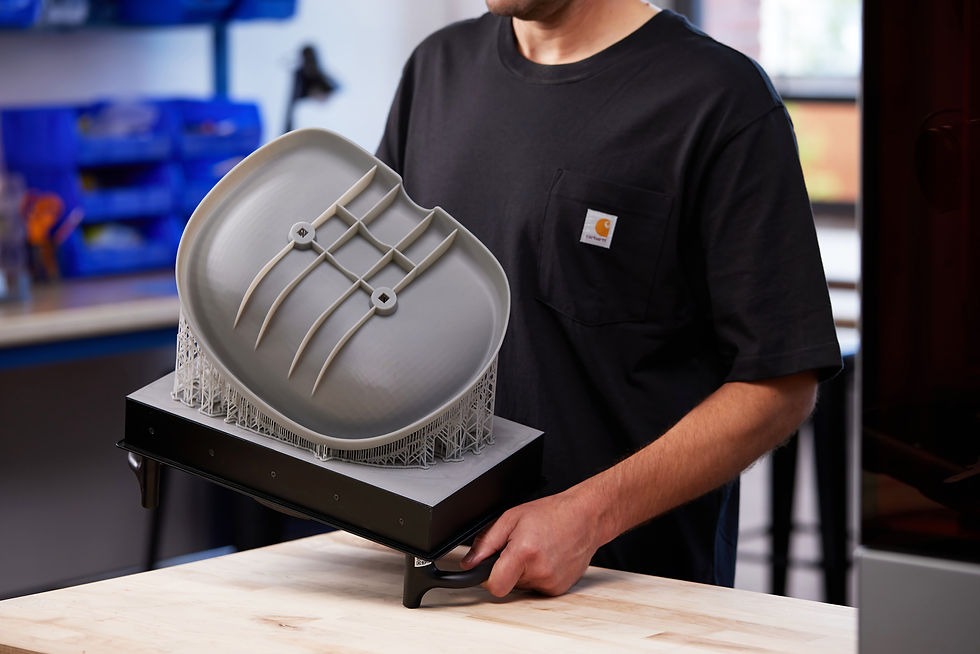
試作を迅速に繰り返し、また大量生産を効率的に行う必要がある製造環境において、Form 4Lは最適なソリューションになります。
LFD技術により飛躍的に向上した造形スピードは、プロトタイピングや製品開発のサイクルを劇的に短縮し、生産効率を高めることが可能です。
さらに、消耗品の耐久性とコスト効率の改善により、長期的なランニングコストも大幅に削減されます。これにより、日々の運用コストを抑えながらも、安定したプリント成功率を維持できる点で、信頼性と経済性のバランスが取れた優れた3Dプリンティングソリューションと言えるでしょう。
Form 4Lは、スピード、安定性、コストパフォーマンスのいずれにおいても大きな進化を遂げており、これらの要素が結びつくことで、3Dプリントのスケールアップを目指す企業にとって最適な3Dプリンターとなります。将来を見据えた高効率な生産体制を構築したい方には、Form 4Lの導入を推奨します。
Comments